
AI Technology Launches a Novel SAC-Based TLPS Solder Paste for Adhesive-Free SMT Components Mounting on 2-Sided PCBs
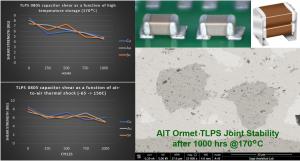
The SMT-8120 soldering-sintering paste, adapted from traditional MLCC paste, provides long-term reliability comparable to established TLPS pastes used in capacitor assembly. The sintered copper also absorbs stress, enhancing performance and thermal cycling.
A novel SAC-based TLPS solder paste enables soldering the 2-sided printed circuit boards components that will not reflow on the second soldering cycles.
PRINCETON JUNCTION, NJ, UNITED STATES, March 6, 2025 /EINPresswire.com/ -- Traditionally, surface mounting components on double-sided printed circuit boards (PCBs) requires adhesive on at least one side to keep the components in place during the wave-soldering or second reflow soldering process. This has been the standard practice since the inception of double-sided PCB assembly.Because one side of the components must undergo the solder reflow process twice, the design of double-sided boards has historically required a non-reflowing adhesive to secure components on the underside. Typically, a SMT epoxy adhesive is used to ensure components remain in place when the board is flipped for the second reflow process. However, if a SAC-based solder paste can form sintered interconnections during the same soldering process without reflowing again, the need for surface mounting adhesive is eliminated. This can lead to increased yields and lower processing costs.
Advantages of Eliminating SMT Adhesive:
The first side of a PCB is usually populated with passive components. SMT adhesive dispensing equipment, adhesive material, and processing add to the costs of circuit board fabrication and complexities. Technically, using an SMT adhesive with a coefficient of thermal expansion (CTE) ranging from 60 ppm/°C below Tg to over 120 ppm/°C above Tg for active components with larger footprints raises reliability concerns. Removing the stress-inducing adhesive allows for greater design flexibility, enabling the use of active components on both sides and reducing the overall footprint of the PCB.
Innovative Soldering-Sintering Solution:
AI Technology, Inc. (AIT), with over 40 years of experience in electronic and semiconductor adhesives, has introduced an innovative application of transient liquid phase sintering (TLPS) solder paste technology through its recent acquisition of Ormet Circuits, Inc. The newly developed SMT-8120 soldering-sintering paste enables adhesive-free surface mounting and interconnections for double-sided PCBs.
SMT-8120 is based on Type 5 SAC solder technology with particle sizes under 25 microns. It utilizes a no-clean flux with a high thixotropic index and can be stored and processed using standard SAC solder paste methods. The paste is screen- or stencil-printable and is embedded with TLPS technology to enable soldering-sintering interconnections. Dispensable formulations are available for repairs and other applications.
Technical Specifications and Processing:
The first reflow process follows a conventional SAC soldering temperature and ramping profile. However, once soldered, the interconnections are sintered, preventing them from reflowing again under the same conditions. This ensures that components remain securely bonded when the board is flipped for the second reflow process, eliminating the need for SMT adhesive.
Reliability and High-Temperature Performance:
The reliability of SMT-8120 interconnections has been validated under thermal cycling and heat-aging tests. Due to the incorporation of copper in the sintered phase, SMT-8120 exhibits superior high-temperature aging stability. This characteristic makes it ideal for double-sided PCB surface mounting in high-temperature applications, particularly in automotive electronics.
Rework Considerations:
Reworking SMT-8120 solder-sintered interconnections requires a modified process. However, for passive components, rework is rarely required in double-sided PCB assemblies.
About AI Technology, Inc. (AIT) and Ormet Circuits, Inc.
Founded in 1981, AI Technology, Inc. (AIT) is headquartered in Princeton, NJ, with additional facilities in Princeton Junction, NJ. Ormet Circuits, Inc., founded in 1991, operates in San Diego, CA, and was acquired by AIT in 2024. SMT-8120 and other TLPS solder-sintering pastes are now available from AIT facilities in Princeton, NJ; San Diego, CA; and soon in Shenzhen, China, to serve Asian customers.
Kevin Chung
AI Technology, Inc.
+1 609-799-8896
email us here
Visit us on social media:
Facebook
X
LinkedIn

Distribution channels: Automotive Industry, Electronics Industry, Manufacturing, Military Industry, Telecommunications
Legal Disclaimer:
EIN Presswire provides this news content "as is" without warranty of any kind. We do not accept any responsibility or liability for the accuracy, content, images, videos, licenses, completeness, legality, or reliability of the information contained in this article. If you have any complaints or copyright issues related to this article, kindly contact the author above.
Submit your press release